
AXONV
Small size, high performance

AXONV
3 AND 5-AXIS MILLING
AxonV is the ideal choice for those seeking uncompromising milling performance with high standards of speed, precision and finish
Versatile, compact and ergonomic, AxonV offers a best-in-class ratio of useful working area to external dimensions.
From prototyping to high-volume series production, it is the milling machine for machining aluminum, brass, technical plastics, composite and advanced materials.
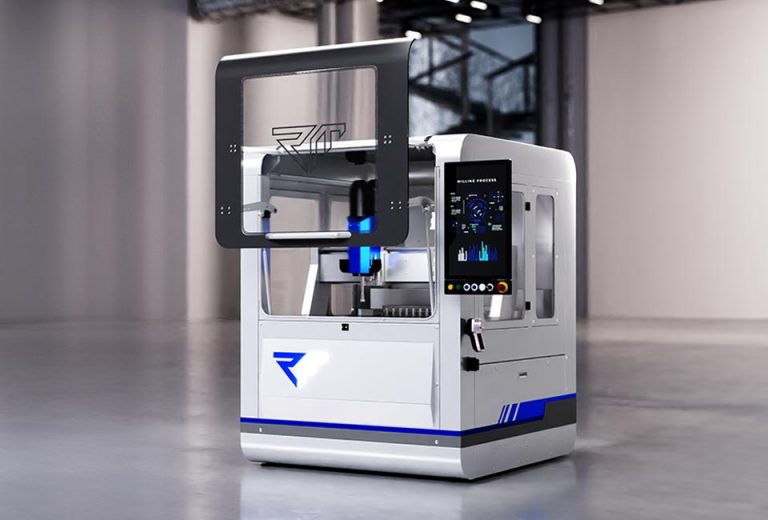

High speed milling
A 4-kilowatt, 40,000-rpm electrospindle provides the power and the ideal speed for high-speed machining. The HSK25 taper coupling ensures maximum performance in terms of rigidity and coupling accuracy.
DISCOVER AXONV
Tool change
AxonV features an automatic tool changer with a capacity of up to 30 positions, which maximizes productivity and reduces downtime. Tool presetting enables automatic tool measurement and check for breakage, ensuring that milling is always precise and uninterrupted.
.jpg)

Cooling
The CNC milling machine's minimal lubrication system precisely dispenses coolant contained in a special tank, directing it straight to the tool and workpiece. This system enables optimal machining on aluminum and light alloys, ensuring optimal cooling and lubrication. This solution does not require coolant disposal management and minimizes waste.
Renishaw probe
Contained in the Z-axis assembly, the Renishaw probe enables fast part measurement and centering. The probe can be engaged and disengaged by the operator and does not occupy positions in the tool changer. There are several benefits with this system: improved quality control, process control, increased machining efficiency, cost reduction and more.

Everything at
your fingertips
The Z-axis assembly includes, protected by a compact anodized aluminum casing, the electro-spindle, the touch probe and the MQL nozzles, both retractable and operable from the control touch screen, and the chip suction hood, adjustable in height to accommodate different tool lengths.

MILLING PERFORMANCE
AxonV features a robust electro-welded frame designed to provide maximum rigidity and strength. This structure effectively reduces vibration and ensures extremely precise machining. The axes are controlled by high-precision brushless motors and recirculating ball screws with 0 backslash, ensuring smooth, repeatable and high-precision movements. Optical scales, a linear measuring system that processes data for better machining, can be installed on the machine axes.

WORKTOPFIXING SOLUTIONS
The work surface (dimensions 805 x 1015 mm), made of milled and ground aluminum, ensures a perfectly flat surface. The machine is equipped with a double fastening system: one by vacuum with the possibility of sectioning and one with threaded steel dowels for mechanical fastening by means of brackets/clamps.
VACUUM FIXING
A worktable capable of holding workpieces by means of vacuum pumps can be installed on AxonV. With vacuum clamping, an under tension is created below the clamped workpiece, and the workpiece is pressed against the clamping plate.
MECHANICAL FIXING
Clamps, screws, bolts, and other mechanical components can be installed to secure the workpiece on the milling machine table. In this way, there is no possibility of sudden movement of the workpiece specimen.

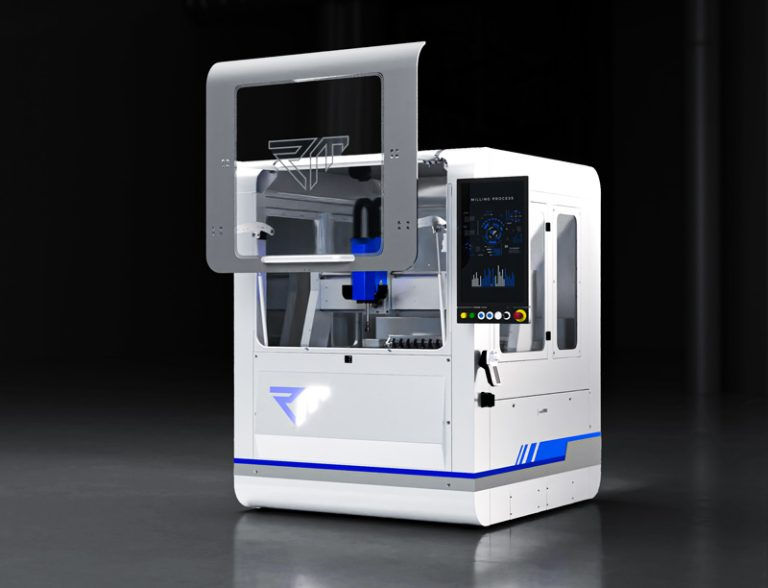
Useful worktable and floor space
To a work surface of 805 x 1015 x 200 mm, AxonV combines small overall dimensions to optimize available space (1800 x 1500 x 1980 mm). These are not altered by the opening of the doors either, with the smaller side doors making little impact and the front door sliding upward.
Mitsubishi CNC control
AxonV has a completely user-friendly and state-of-the-art control.
The hardware consists of a swiveling console with a 27-inch touch screen panel. Machine programs, based on the Windows operating system, are adjusted by the Mitsubishi control unit. It provides flexibility of use and high performance for different types of applications and material processing. The HMI puts all the controls of AxonV under control and allows in particular to: import machining files, analyze the design from the 2D/3D preview, and start machining. This is combined with an electronic handwheel to manually control axes and speed.
.jpg)

Suction and management of milling residues
A dual system for handling milling waste ensures maximum cleanliness of the working area. A height-adjustable hood that can be connected to an external vacuum is installed on the electro-spindle of Axon V to effectively collect chips. A special system conveys machining residues into a dedicated container for easy disposal.