
XTEND
CNC milling machine for large plates
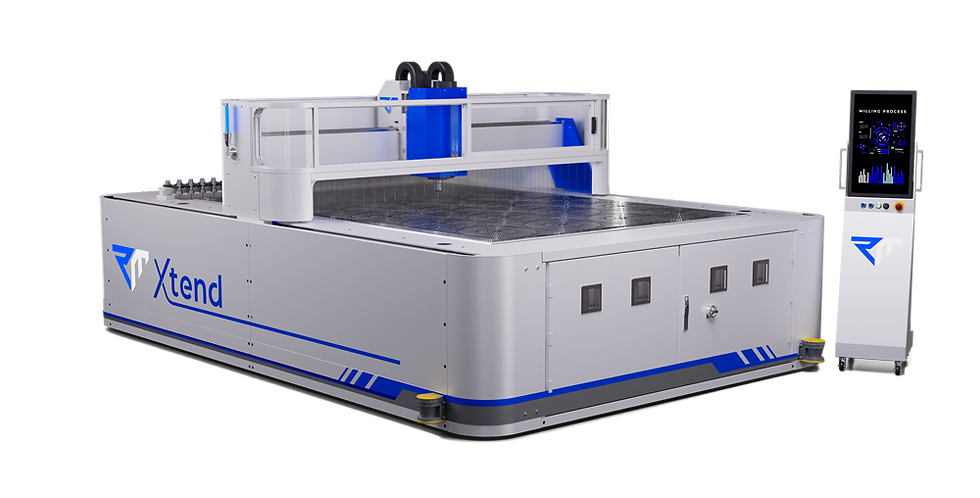
XTEND
Xtend is the versatile CNC milling machine that is ideal for those seeking large-format plate machining and fast, accurate nesting, with very short tooling and part positioning times.
With working areas up to 4000 x 2000 mm and high-speed milling and rapid handling, it is ideal for processing aluminum, nonferrous metals, composite fibers and plastics.
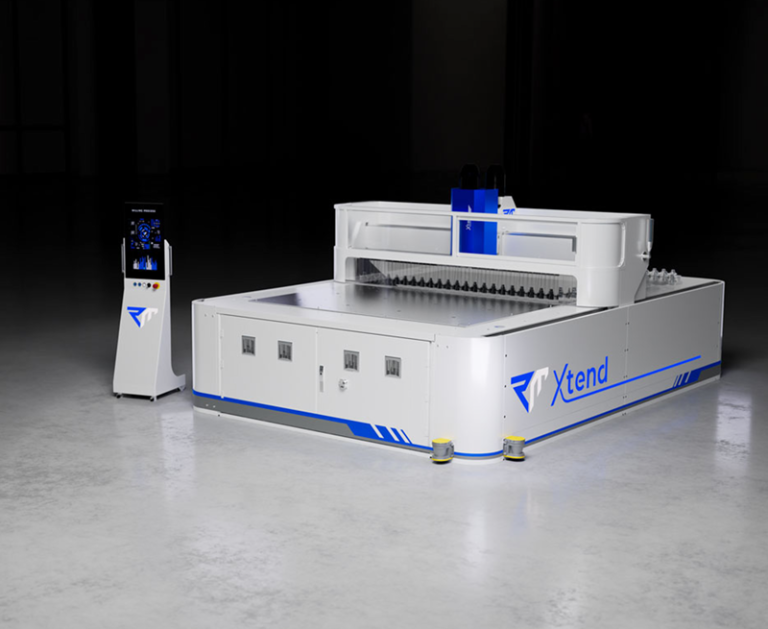

Electrospindle available in two versions:
-
8kW at 36,000 rpm, with HSK40 attachment, for high-speed machining and excellent finish levels for machining with even small-diameter tools.
-
14 kW at 24.000 rpm, with HSK F63, for high removal milling and deep, precise passes with large tools.
DISCOVER XTEND
Configurations and accessories to meet every need
Tool change
Xtend is equipped with an automatic tool changer rack with capacity for up to 50 positions, which maximizes productivity and reduces tooling time.
Together with the tool magazine, there is a tool length measurement and tool breakage control system, which is essential for ensuring long unattended machining and very short set-up times.

.jpg)
Cooling
The minimal oil and/or air lubrication system, adjustable in delivery frequency and flow rate, ensures timely cooling of the contact surfaces, optimizing the tool life cycle. This solution does not require coolant disposal management or the use of collection tanks.
Renishaw probe
The Renishaw probe is contained in the Z-axis assembly and it enables fast measurement and centering of the workpiece, even during roto-translation. The probe is housed alongside the spindle, which can be activated by the operator directly from the control panel, without committing stations in the tool changer. Due to its location, the probe is immediately available, without having to activate tool change procedures.

MILLING PERFORMANCE
Xtend is built on a base made of electro-welded steel tubulars. Its rigid structure and excellent axis dynamics guarantee and excellent performance in milling on plates of various materials and nesting operations. The axes are controlled by brushless motors with absolute encoders and racks that ensure smooth and precise movements.

WORKTOPFIXING SOLUTIONS
The work surface, measuring up to 4000 x 2000 mm, made of thick milled and ground aluminum plates, ensures a perfectly flat work surface that is resistant to impact and stress.
VACUUM FIXING
Xtend is equipped with a worktable that can hold workpieces by means of one or more vacuum pumps to ensure the best possible clamping. The subdivision of up to 32 software-selectable zones allows both large and small slabs to be clamped on the table.
MECHANICAL FIXING
Threaded inserts are available on the worktable on which mechanical clamping systems such as vices and clamps, pneumatic or manual, can be installed. The modularity of the worktable, which is divided into zones (up to 32), allows mechanical workpiece clamping and vacuum holding systems to be used simultaneously in different areas.
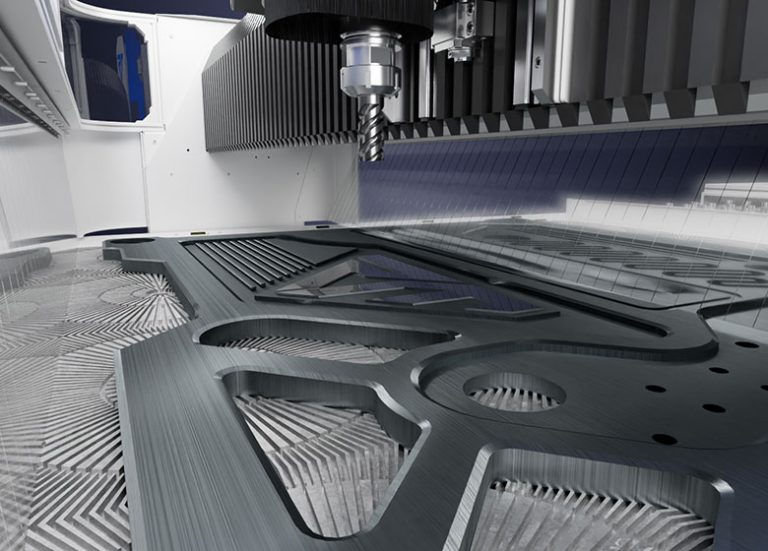
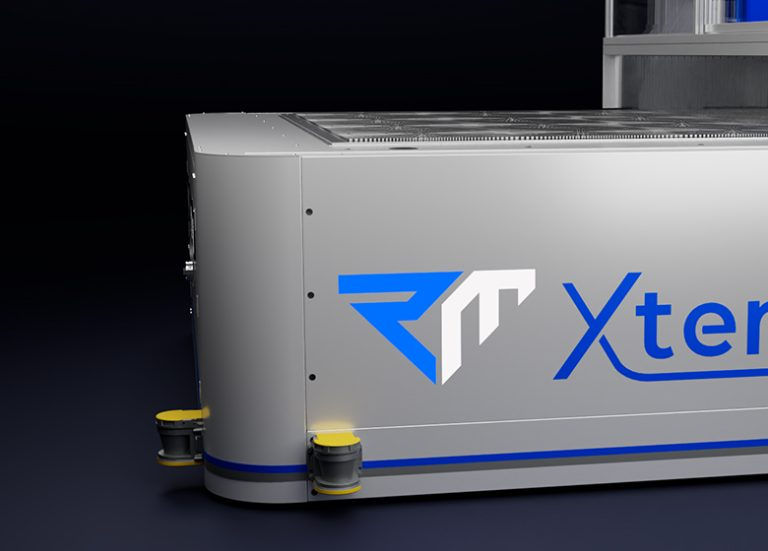
Safety
In addition to the protective barriers installed on the bridge, which are essential to prevent possible projection of objects (tool or chip), the machine is equipped with a laser scanner system with a double safety zone. The first reduces, when it is exceeded, the speed of the axes. The second activates the immediate blocking of the machine if a potential hazard is detected.
Mitsubishi CNC control
Xtend is powered by a state-of-the-art Mitubishi CNC. In addition to numerical control and axis motors, the system includes a swiveling control console with a 27-inch, Windows-based industrial touch screen PC. This system allows the operator to easily manage to machine controls, use CAD and CAM programs directly on the machine, and access the company network.

.jpg)
Suction and management of milling residues
Xtend is equipped with an advanced milling waste management system that always ensures a clean work area. The electro spindle is equipped with a height-adjustable hood designed to be connected to an external vacuum system, thus ensuring effective collection of chips and dust generated during machining.